For optimal process control and to take advantage of the possible benefits of the employed reactor concepts, obtaining information of the local reactant concentrations for H2, O2 and H2O2 is vital. So far commercially available analytic systems are only able to gather information about the reactant concentrations at the outlet of the synthesis reactors, which makes it challenging to define and optimize process parameters of such a microreactor system.
At the Laboratory for Sensors (IMTEK) an electrochemical microsensor system for the continuous measurement of H2O2, H2 and O2 in microreactors is developed as part of this subproject. Electrochemical sensors hold a high potential for the use in microreactor applications as they allow for exact measurements of even small concentrations changes due to their high sensitivity, selectivity and defined zero points. Thanks to very small electrode sizes, microelectrode arrays as amperometric sensors are suitable for in-situ measurements with high spatial and temporal resolution and thus allow for parallel monitoring of the substance concentrations at different points in the reaction channel in real-time. Currently, 300 µm platinum electrodes are used to measure at four points over a channel width of 4 mm. Arrays of platinum microelectrodes were integrated into a robust epoxy sensor body (plug) that can be mounted in the microreactor. This allows for simultaneous measurements at up to 8 different positions inside the microreactor for an online feedback of the reaction and process control.
|
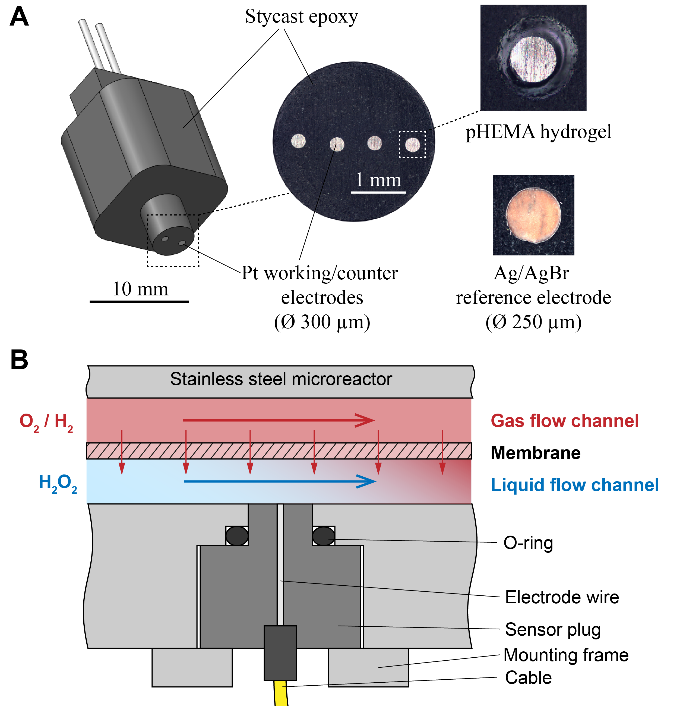 |
|
|
Fig. 3: Microsensor design and housing (A). Schematic of the membrane reactor principle and sensor placement inside the microreactor (B). |
The main challenges and criteria for the development of the sensor system are selectivity, linearity at high concentrations and measurement in the presence of halide ions and catalyst particles in the microreactor. Therefore, new amperometric and chronoamperometric protocols were developed, and the employed platinum electrochemistry was investigated under reactor conditions. Furthermore, the constant presence and concentration of the halide ion bromide was used to develop an on-plug silver/silver bromide reference electrode by galvanic modification to ensure a stable measurement potential. The modification of the platinum electrodes with a diffusion limiting membrane of poly(hydroxylethyl methacrylate) (pHEMA) hydrogel enabled the extension of the linear detection range, by controlling the mass transport to the electrode. An as modified electrode is able to linearly measure H2O2 concentrations in the reactor up to 20 mM, while still achieving a detection limit in the low mircomolar range. It was shown that our microsensors were able to measure elevated concentrations of dissolved reaction gases O2 and H2 und process conditions and pressures of 70 bar linearly up to 52 mM and 40 mM, respectively, without any loss in sensitivity when compared with measurements at atmospheric pressure. The electrochemical measurement at such high pressures and with the resulting high concentrations up to 50 mM has not been demonstrated before in literature. By mounting four of our microsensor plugs into the membrane rector, gas dissolution was observed for the first time in situ and in real-time. The system was able to spatially resolve the change of gas dissolution, depending on the relative positioning to the gas stream inlet, through the reactor membrane into the liquid phase by applying gas mixtures with different O2 content. Challenging selectivity for the simultaneous detection of H2O2 and O2, which both are reduced at the same potential, could be resolved by the use of sophisticated chronoamperometric protocols, which allow to deduct the H2O2 oxidation current measured first from the superimposed O2/H2O2 reduction current to obtain a selective measurement current for the detection of O2.
|
 |
|
Fig. 4: Hydrogen peroxide calibration curve with a platinum-based microelectrode modified with pHEMA membrane showing high precision and linear behavior up to 20 mM. |
|
|
Fig. 5: Dissolved hydrogen calibration curve at normal pressure (A) and at 70 bar (B) showing no loss in sensitivity. |
|
Fig. 6: Dissolved oxygen calibration curve at normal pressure (A) and at 70 bar (B) showing no loss in sensitivity. |
|
Concentration patterns in meander channel
In order to spatially and temporally resolve the concentration profile of the reactants H2, O2, H2O2 in the flow of the meander-shaped channel, 13 boreholes for sensor integration were drilled in the channel in order to cover as wide a range of the reactor as possible. In the first tests we integrated four sensors in the centerline of the reactor and closed the other nine boreholes with dummies.
|
Fig. 7: The integration of several sensor plugs enables the in situ measurement of the local reactant concentrations H2, O2 and H2O2 along the entire reactor channel. |
|
At an operating pressure of 10 bar, we observed the saturation of oxygen versus nitrogen in the meander channel in the aqueous electrolyte containing sodium bromide and sulfuric acid at a flow rate of 1 mL/min. First both gas dosing zones were flushed with nitrogen and after t = 100 s one gas was switched to dosing of pure oxygen. By controlling the sensors with chronoamperometric measuring protocols, it could be shown that in the meander channel at position no oxygen reaches the channel bottom, because the diffusive mass transport of dissolved gases is overlayed by the convective transport. Furthermore, the measurement confirmed the expectation that starting from position 2 to position 4, the intensity of the current signal drop decreases proportionally to the oxygen concentration, revealing the dynamics of dissolution within the microchannel reactor.
|
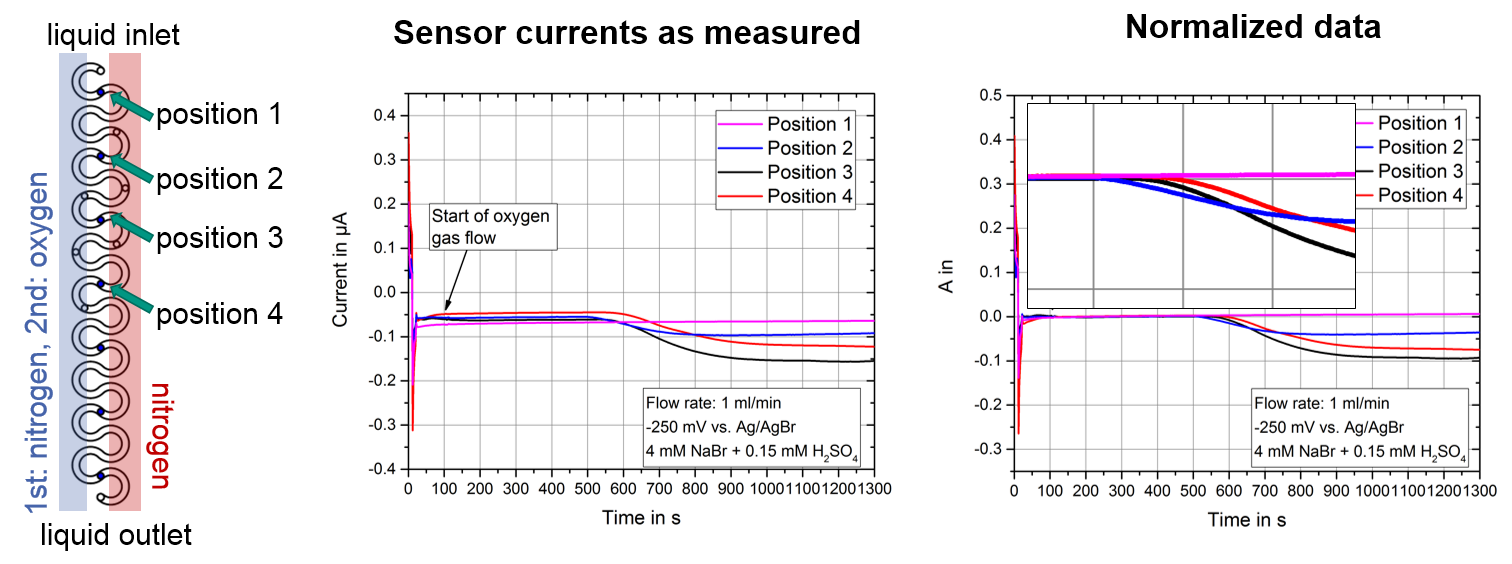 |
|
|
Fig. 8: Exemplary measurement of the progression of dissolved oxygen in the meander channel at four points. The normalized data show the temporal evolution of saturation from the beginning to the end of the reactor as well as an increasing oxygen concentration with temporally stable signal behavior. |